► A look inside VW’s first electric car factory
► First sight of ID.3 production in progress
► Zwickau factory’s transformation for MEB
From a distance, it looks like the sort of visual definition of a factory you might have drawn as a child: long, oblong buildings with two big cylindrical chimneys and the company name writ large on the side – in this case, Volkswagen.
The Saxony town of Zwickau has been a bustling car production site for more than a century. Horch cars were built here in the 1900s, and Trabants mass-produced from the 1950s all the way until 1990. Since 1991 Zwickau has been an epicentre of giant-scale production for the Volkswagen Group: from Golfs and Passats to Phaetons, Bentleys and Lamborghini Urus bodyshells.
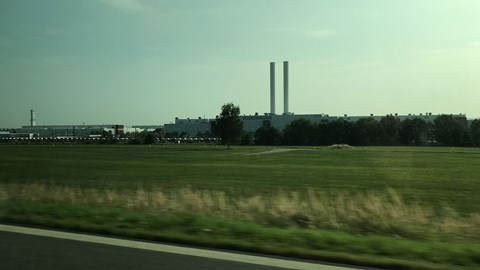
Now, it enters a new, and crucial, chapter in its history: Volkswagen is in the process of converting its Zwickau plant into a factory dedicated purely to electric car production. It will be the first site for production of the company’s new ID.3 mass-market electric hatchback, along with further EVs for Seat and Audi.
CAR was among the first journalists in the world to visit the Zwickau factory as it undergoes its transition, and witness the first VW ID.3 cars traveling down the production line. Full ID.3 production gets underway here in November 2019.
Zwickau: from ICE to EV
A ‘legacy factory’ being converted to purely electric production is quite a statement for the company, and VW is keen to communicate it.
Not least because, had the Dieselgate furore not erupted in 2015, Zwickau may have merrily continued turning out several hundred thousand Golf hatchbacks and estates per year alongside various other internal combustion engine (ICE) models for various brands within the group.
The decision to turn Zwickau into an EV plant was taken in mid-2016, we’re told by Thomas Ulbrich, board member for e-mobility for the VW brand. Zwickau will be ‘the nucleus’ for the ramp-up in EV production, he says.
While further factories around the world are also being modified for production of MEB models (standing for Modular Electric drive Matrix, VW’s new platform for purely battery-electric vehicles), Zwickau will be the largest and ‘highest-performing’ in Europe, Ulbrich says.
‘Some plants will be completely transformed, we’ll have one plant which was just transformed by a half [with] production of ICE cars and EVs. We [will] also have in China one plant which is completely new only for MEB cars.’
Eight MEB locations will be set up worldwide by 2022, including sites in Europe, the USA and China, but Zwickau is Genesis for VW’s new electric push, and described by Ulbrich as ‘the largest and most difficult plant transformation.’
Ultimately, the transformation of the Zwickau plant for MEB production is calculated to require an investment of more than €1.2bn. So far, VW says €880m has been invested in the site’s conversion. Total investment into electric car production across the group by 2023 is calculated to be in the region of €30bn.
The transformation timetable
In 2020, production of electric cars will outnumber that of ICE cars at Zwickau; in 2021, there is no more ICE production scheduled and MEB production will be in full swing.
The VW ID.3 is the car that will really kick things off at Zwickau, but it will be one of six electric models across three brands to be built at the plant – three VWs, two Audis and one Seat. While not mentioned by name during our visit, the latter will be the Seat el-Born sister car to the ID.3.
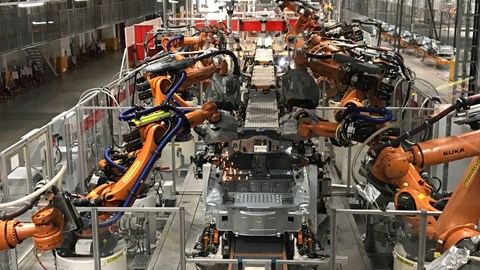
Five new buildings are complete, and seven more under construction, while existing buildings are being retrofitted with extensions and annexes.
So far 400‘pre-series’ ID.3 cars have been completed. A total of 2000 pre-production cars will be built, for crash testing, endurance testing and to ensure the production process is fully water-tight before full-scale production begins in November.
VW ID.3 – the first cars roll down the line
We watched some of the first few pre-series ID.3 cars coming down the line at Zwickau and got a first-hand view of the build process.
The final production hall is a curious juxtaposition. The final production run of the Mk7 VW Golf is currently being completed at Zwickau, and Golfs and ID.3s travel down adjacent conveyor belts alongside one another. It feels symbolic; on one belt, a soon-to-be-replaced ICE model, and alongside, the brand-new electric model the company is pinning many of its hopes (and billions of Euros) on.
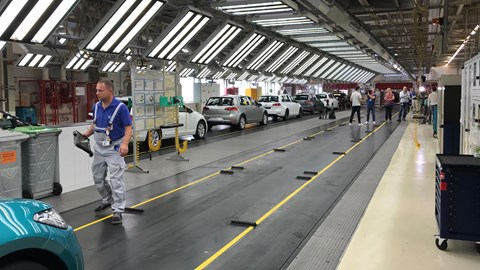
While there’s a steady stream of Golfs, there are bigger gaps between ID.3s as production gradually ramps up. Once it’s in full flow, one new ID.3 will cross the finish line every 90 seconds. At the moment, around six to eight pre-series ID.3s are completed per day.
The ID.3 up close
Thomas Ulbrich says it was a key objective for the ID.3 to have a price comparable to a diesel Golf today, and the ID.3 will retail below €30k.
On the final assembly line, the ID.3s emerge from a monsoon booth where they’re subjected to six minutes of heavy rain so the production line staff can check the seals for any leaks. It’s a tall car; the ones we see are on 20-inch wheels but they look relatively small in the context of the car’s deep sides and tall roofline. With the door open, you can see how tall the floor section is to accommodate the battery section.
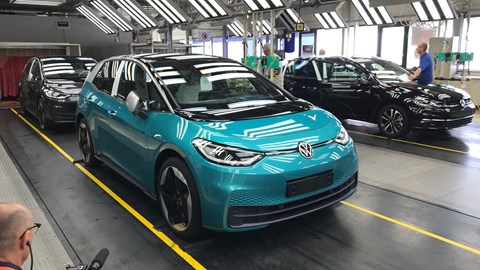
In the next section of the factory, Hall 5, we’re the first members of the press to see the main ID.3 production line, where the MEB platform is ‘married’ to the bodyshell.
‘This hall looked completely different two months ago,’ says Dr. Carsten Krebs, communications director for the factory. ‘The entire floor was ripped out over the summer break and refitted.’
The ‘wedding’: MEB platform meets ID.3 body
VW staff refer to this section of the line as the ‘wedding’ station, but rather than a chapel it’s the point at which raw MEB platforms are married to the ID.3’s body shells.
The shells are carried high above the line in cradles, and the MEB modules, with suspension already attached, wait below. The shell (already fitted with the dashboard and certain interior elements) is lowered onto the chassis, and giant screws are robotically inserted beneath.
On a conventional car, the exhaust system and elements in the transmission tunnel might ordinarily be installed at this point. No such need here, and ultimately, VW will be able to make ID.3s quicker than it did the Golf, with production capacity expected to increase from around 1350 to 1500 vehicles a day.
It travels to the next stage, more screws are inputted by robots stoically, methodically bending their arms to the task at hand, before human technicians step in to complete the process.

In total, there are 10 steps and once production is at full speed, the ‘wedding’ takes only 1.4 minutes.
Further along, the car has almost reached the end of the line and technicians measure the gaps for the bonnet and door, and apply the VW badge – significantly, the new, redesigned one – before the car goes off to get a bath in the rain testing bay and join the Golfs in the final check hall.
Zwickau features 8000 employees, and virtually all of them will continue to work here once the factory becomes a pure MEB production site, with minimal redundancies, Ulbrich says.
That has meant a great deal of retraining, with thousands of training and retraining programmes to be organised. This year alone has featured 13,000 training sessions.
Read more about future electric Volkswagens
The body shop
In the next building, however, the scene is mostly robots. Hall 2, the body shop centre, is the largest in the factory with a square surface equivalent to around 11 football fields.
In readiness for the ID.3 and other MEB models, VW has spent €400m on this part of the factory alone. It’s not hard to see where the money has gone; nearly everything here is new, including 1625 fresh robots. They work in a constant, whirring ballet that’s part-elegant, part-spooky, and entirely noisy. Huge spot-weld robots swivel in and go to surgery on partly completed shells as they travel down the line. A hot, acrid smell fills the air, there are flashes and fizzes, and the shell is spirited along to the next bay for more of the same.
There are four separate body shops within the hall, including one for the Mk7 Golf as its production winds down. We see stacks of body panels, including multi-packs of the instantly recognisable Golf’s C-pillars.
Approximately 1000 people work in the hall in a three-shift system, which will stay the same in the post-MEB era. Previously a lot of employees would have completed many of the tasks in here by hand, we’re told, and now staff are learning alternative jobs from scratch. Some of them are more than 50 years old, and hadn’t previously expected to retrain in a new role – one of the many unforeseen ripples from Dieselgate.
Volkswagen’s factories make it the largest employer in Saxony, with 10,000 people across three sites: Zwickau (8000 people), Dresden (400 people) and an engine site at Chemnitz (1600 people).
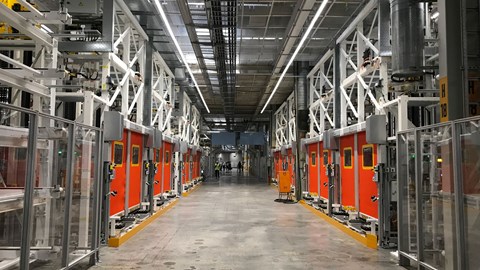
VW’s hand might have been forced into pushing its electric programmes forward more by the political climate post-emissions scandal than by the physical climate, but it is jumping in with both feet. The depth of redevelopment at Zwickau is indicative of that.
Furthermore, VW claims that the process of ID.3 production itself is, as far as possible, carbon neutral. Thomas Ulbrich told CAR: ‘Our promise is if we take an MEB car like the ID3, the car will be CO2 neutral by the time of handover to the customer. That means that we are investigating deeply in the supply chain, for example for battery cells, we have a contract with our suppliers that they already use regenerable energy in their production. We also changed the energy resources in our plant in Zwickau to use green energy.’
VW acknowledges that a certain amount of CO2 emitted by production cannot be completely avoided, but will be compensated for by ‘internationally accepted and certified projects.’
As for the MEB platform itself, with so many models hinging on it, its scope for longevity and flexibility is key. Thomas Ulbrich told CAR: ‘Volkswagen is a platform professional. We started already in the 1990s to qualify ourself for developing platforms for long time periods and to be usable for all kinds of bodystyles, and MEB is the next evolutionary step to bring these capabilities to the electric mobility world. The MEB platform is able to cover cars from the A-segment until future B-segment, and body styles from concept cars up to buses.’
By 2028 Ulbrich says there will be around 70 new EV models in the group’s portfolio, by which time VW estimates it will have manufactured around 22 million electric cars. These will include the upcoming Porsche Taycan Cross Turismo and Audi e-Tron GT, along with the ID.3’s MEB siblings, including saloon and a campervan-style variants, previewed by the ID. Vizzion and ID. Buzz concepts respectively.
The key question is how well the MEB cars will drive, and if they will meet with commercial success great enough to pay back the gargantuan investment in Zwickau and the seven other MEB plants worldwide. We’ll know the answer to the first question soon enough; the second will take longer to determine.