► The future of car batteries
► Formula E and cell tech
► Williams R&D chief tells all
Williams’ R&D Paul McNamara on how Formula E is driving the development of better batteries for road cars.
> Williams Advanced Engineering is trying to take stuff that’s come from motorsport, and apply it into the normal industrial environment: automotive, technology, aerospace, health and sports sciences. Automotive is the biggest part of our business, and there’s a direct link to the batteries we’ve been supplying to all Formula E teams and what we can do on road-car batteries.
> Formula E is now in its third season, and we’ve been learning all the time, making improvements to robustness, reliability and manufacturability. We’ve applied what we’ve learnt to road-car programmes such as the Aston Martin Rapide E and Nissan BladeGlider concept.
> Formula E road tracks are very bumpy; it bounces all the components around a lot, and has taught us how to insulate battery cells from vibration. The batteries are very highly maintainable, which is unusual in a road car, but in a racecar that allows you to strip the battery down at the racetrack, remove components, make some fixes.
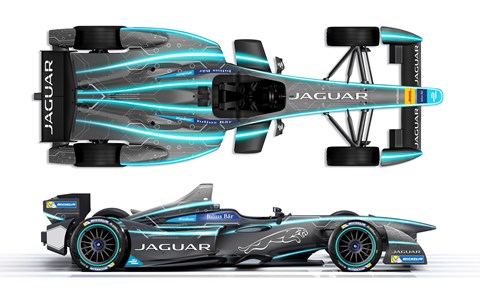
> Range is effectively a size and weight trade-off. Cells have a basic kilowatt hour stored per kilo, and the chemists are working away on that, making big strides the whole time. We can probably expect kilowatts per kilogram growth at a base chemistry level of 5-6% a year. It’s not going to go on forever, but at the moment I think the gains remain quite big.
> The biggest single range drainer is climate control, and we’re developing various strategies for that. As soon as you start using a battery, it begins to warm up; so we’re looking at storing some of that heat in glorified vacuum flasks, to use that to heat the car.
> We’ve done projects with other chemistries for batteries, but right now the industry is pushing ahead with lithium-ion, and the economies of scale start to come from that. I do see a period when lithium-ion will start to define how the cars are designed and set-up. Then other battery technologies will start to become disruptive techs, but they’ll have to show substantial benefits as lithium-ion will start to develop an industrial base.
> 60% of the battery is comprised of cells, 40% is other stuff, like the safety cage, the control system, cooling system, the electrical connectors that are quite heavy because batteries are handling big currents of 350 amps for Formula E, but up to 600 amps in some cases. We’re getting cleverer at the design as we get more experience from the duty cycle, and that’s why motorsport is such a great benefit to us.
> We’re working on battery packs for premium road cars; at 600-700kg they’re getting on for a third of the weight of the car. Most people are targeting up to 300 miles’ range; Tesla set the market expectation. Our challenge over the next five to 10 years is to get the range up to 400 miles or so, or get the pack weight down by 20-30%. If we can get that 20-30% improvement, we’re at a tipping point to electric vehicles becoming practical.
More car tech stories