► New innovations transforming our world
► We look into the world of 3D printing
► We ask those companies who are using it
Blowing James Bond’s DB5 to smithereens in Skyfall was sacrilegious, except that the Aston was a realistic one-third scale model made using 3D printing, the same technology that churns out thousands of low-cost bespoke hearing aids and that enabled Joel Gibbard, winner of this year’s James Dyson Award, to make an inexpensive custom-fit prosthetic hand in less than two days.
Such is 3D printing’s anticipated impact across manufacturing that The Economist has dubbed it ‘the third industrial revolution’, likely to have a similar impact on manufacturing as Henry Ford’s production line for the Model T in 1913.
Jaguar Land Rover and 3D printing
JLR is in the motor industry vanguard embracing a technology that is revolutionising the way cars are designed and tested. ‘In 1992 we were among the first adopters of 3D printing,’ explains Mark Barrington, JLR’s prototype and tooling manager. ‘In those days the processes weren’t that capable but we could see the potential, and we’re realising that today.’
‘Wheel proposals used to be modelled in clay – a single wheel could take 10 days,’ says Jaguar’s director of design Ian Callum. ‘Now we can print a full-size 22-inch wheel in a matter of hours. That’s a huge saving in time, but 3D printing also ensures accuracy.’
JLR prints some 55,000 parts a year, at a cost of £1 million in materials. Printed components range from replica radiator grilles for validation models through to more fragile switchgear, key fobs and door-mirror casings (see illustration) for one-off concept cars.
The reason for 3D printing’s rapid rise from intriguing novelty to design and engineering must-have, says Barrington, is simple: time. When an OEM is developing a new car, time to market is of the essence. Get a new car into the showroom more quickly and you save money and slash the waiting time before revenues start rolling in.
How does 3D printing work?
Traditionally, many prototype components such as door handles, air-conditioning vents, trim and binnacles have been laboriously hand-crafted or produced from prototype tooling, a process that could take weeks or even months.
Now, a 3D printer can turn a computer aided design (CAD) file into a prototype part without tooling. Parts are produced in a fraction of the time, once they reach the front of the print queue (a day or two at JLR). This enables design iterations to be evaluated and tested rapidly as engineers and designers seek optimal solutions. Because 3D printing’s also an additive process – material added rather than machined away – there’s no waste.
‘On the engineering side, 3D printing is extremely useful for looking at the manufacturability of a proposed component,’ explains Jaguar F-Pace vehicle line director Kevin Stride. ‘You can do anything in CAD, but that doesn’t always translate into an assembly that’s real-world feasible. With 3D printing we can create the parts in question quickly, call people in from engineering and production to check that what we want to do is feasible. It’s come a long way – a few years ago we could only print small parts.’
JLR uses four types of 3D printing, depending on the job. Polyjet modelling and stereolithography are used for detailed components such as dials and switches – polyjet printers spray 30-micron thick layers of polymer resin which are then hardened by a scanning laser to build up the part; stereolithography sweeps a laser across a vat of resin, building the part up one 100-micron layer at a time. Laser sintering fuses thicker, 120-micron layers of nylon powder using a laser. In fused deposition modelling (FDM), layers are laid down in tough ABS plastic.
For now cost means 3D printing is a technology for design and engineering rather than production, though Barrington believes there are opportunities for halo products and personalisation: ‘We could add high-value content to a small number of vehicles – that’s when the public will start to see more automotive 3D printing.’
The process
1) The process starts with a CAD model of the component. The model can be rendered and viewed on-screen but that’s no good for a design review…
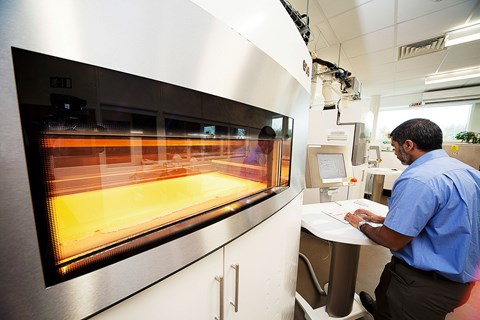
2) The CAD model’s data is transmitted directly to the 3D printer, which gradually builds up the part in layers as fine as a human hair. A laser scans across the material, fusing it together and building the component.
3) Because 3D printing is an additive process, only applying material where it’s needed, waste is considerably reduced compared to traditional modelling methods.
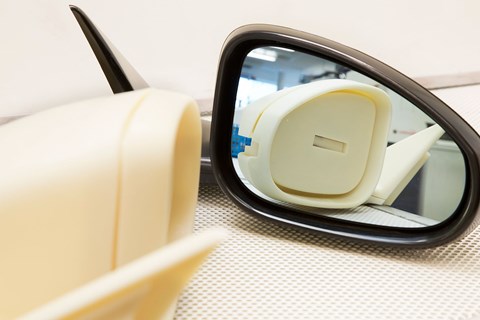
4) The part, in this case a wing mirror, is finished in hours, versus days or even weeks by other means. It’s ready to be fitted to a clay for a styling review.
Read more CAR tech news