► Inside Bentley’s Crewe factory as it shuts down
► CEO Adrian Hallmark on planning to restart
► How has product development been affected?
Bentley will take its Crewe factory out of suspended animation on Monday 11 May 2020, beginning a week-long ramp-up to restart production. But what’s been happening behind the scenes, to steer Bentley through the seven-week shutdown necessitated by the Coronavirus pandemic?
For chairman and CEO Adrian Hallmark, every business day began and closed with a crisis management meeting. ‘The morning one is to reflect on any news that’s come in relating to suppliers, our colleagues, any illnesses, any deterioration in the two people who caught the disease, both hospitalised, both released and fine.
‘Then we have a sleeves-up, operational discussion about the [factory] restart – and what will we do to make the best of 2020, based around having a hole in it bigger than the profit we planned.’
The car industry and coronavirus: an explainer
How to remotely plan a factory restart
The CEO is talking to CAR by video call in late April from his family home in France. When the factory was wound down to just being operated by a skeleton crew of around 200 (5 per cent of the workforce), social distancing guidelines required Hallmark to work remotely.
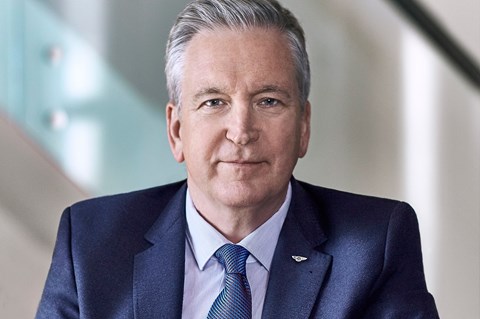
Logistics, purchasing and manufacturing teams were doing likewise, hurriedly compiling an enormous timing chart of 500 suppliers and when they could be active again. This included Volkswagen Group operations too, because Bentayga bodies-in-white and V8 engines come from plants in mainland Europe.
Bentley can now hold seven days of stock – up from two thanks to warehousing revisions triggered by Brexit – and with this in mind the company pinpointed 11 May as the date when reawakened suppliers and the factory could begin running in unison again. While the Tier 1 suppliers have been able to make it through the shutdown, the middle tier would have begun running out of cash with a longer hiatus.
Naturally the most vulnerable are the smallest 5-10 per cent of Bentley suppliers – any businesses going under would have forced rapid-fire new sourcing. ‘We don’t see a strategic risk with the supply chain but we do see massive pressure,’ concludes Hallmark.
When Crewe was mothballed in March
Before his return in early May to spearhead the factory restart, the last time Hallmark entered the assembly hall was Tuesday 24 March. ‘Every car was covered with plastic bags,’ he recalls. ‘The place was spick and span. A few people were in the final assembly area, with probably six or eight cars in there. And there were a few people in maintenance. Everybody I walked past and spoke to, they were gutted.
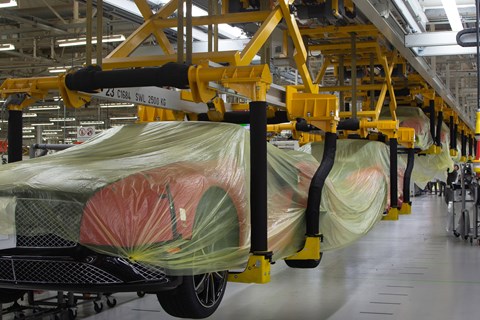
‘The way we’d revved everybody up for two years, and the formula we’d built was so clear and we’d involved them in everything. Everybody felt exactly the same. In the end it’s only business, it’s not like losing somebody to Covid-19 but the passion, the effort, the energy, that people put in to get us to that position, and to have it ripped away, everybody was disappointed, frustrated.’
How Coronavirus has affected motorsport
What’s the impact on Bentley’s finances?
Bentley was expecting 2020 to be the best year in the company’s 100-year history: production for the year is pretty much sold out, despite the manufacturing team hastening build time by 24 per cent. The company was gunning for record sales and record profits. Now the board is monitoring the company’s cash position on pretty much a daily basis, as it seeks to stem the losses.
‘While we have enough funds and the resources to keep us going, our costs are about £20 million a week, when you’re getting zero revenue it bloody hurts,’ reflects Adrian Hallmark.
‘The mood change is from controlled euphoria and a determination to deliver the full potential of the brand to back into survival mode. What do we do to protect our colleagues, the company, the future investment and the customers? What do we need to do this year, to cut costs, to do things differently and to defer certain things? We’ve ruthlessly prioritised everything we’re doing.’
How did Coronavirus affect Bentley product development?
While operations took up a mighty proportion of the board’s crisis-management time, the CEO could occasionally escape into the product world by digitally connecting with the design department. At one such meeting, design director Stefan Sielaff and his team took the board through kick-off ideas for a replacement model, showing sketches, images and mood boards with 30 people calling in remotely.
The engineers were also able to keep new car and technology projects moving forward. Stress analysis, packaging studies, working with suppliers to mature parts and delivering a manufacturing plan – such work progressed. However testing work, involving third parties such as emissions labs or proving grounds, ground to a complete standstill.
‘If you take any engine derivative or emissions testing process, they are all delayed, all the labs are closed. What we are talking about is weeks to months of delay, not years. But it means we may not get all the certification done in time this year for when certain legislation comes in place, and it won’t be just us.
‘All Bentley’s car projects continue, there’s nothing been cancelled. But I’m sure we’ll have to delay certain programmes. One technology, one derivative we’re planning, if we don’t get it done before say September 2021, then it has to go through a whole new certification process like a new car. There are three or four things like that, where if we don’t have time to do the validation at the end then the derivative won’t be available.’
Revised processes to restart Crewe production
Bentley has rolled out 250 new hygiene and social distancing measures for staff returning to work. Employees’ temperatures are taken as they arrive on site, face masks and 2-metre social distancing are compulsory, and new arrival systems and one-way walking flows help minimise contact.
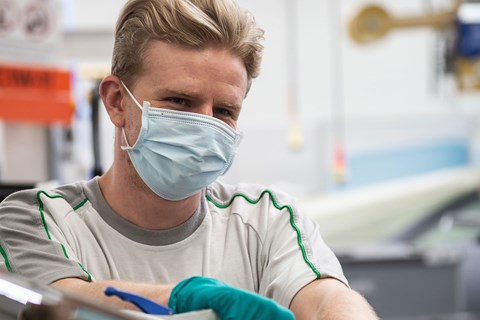
Massive changes have been implemented in the assembly hall. ‘We won’t come back from zero to 100, it’ll be a ratcheted approach probably over 6-8 weeks,’ Adrian Hallmark told Car in late April. ‘For a 50 per cent production period, we may have to leave a car out every second car. Hit one, miss one, so do one phase of work over two stations, so we can separate people that would normally be working on the same station.
‘You can imagine how complex that is with the components and tools we’ve just laid out to take 24 per cent out of the build time. We’ve got to replan all of that detail in a four-week period which is a monster challenge.’
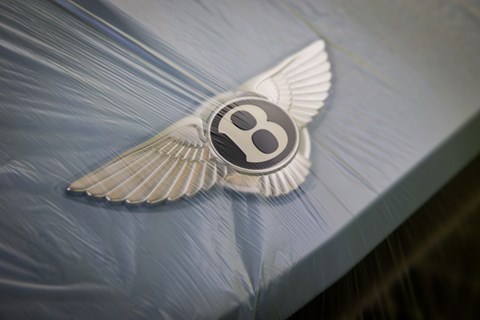
What will Bentley Motors look like in 12 months’ time?
Bentley’s chairman and CEO admits it’s been an incredibly challenging period, even for someone who went through Porsche’s crash from producing 63,000 to 13,000 cars in the early 1990s. ‘Without question, the speed and the depth of this stoppage, I’ve never seen anything like it before. If we get a Hard Brexit in December, I’d just drop the mic. We won’t be right by December.
‘We’ve got plans, we’ve done so many scenarios I’m sick of scenarios! May 11 we may ramp in our planned way, then we get a vaccine, and next February everyone’s spending money because of pent up demand.
‘But another scenario is this completely recalibrates government funding, company balance sheets and customer expectations, and the virus comes back again and we haven’t got a vaccine that effectively controls it, the variability of those scenarios is so great.
‘The key thing in a situation like this is you’ve got to be flexible, never say it can’t get worse. Because it can. But you should always plan for the better.’