► Why car makers are scrambling to help
► Can vehicle factories make ventilators in time?
► Car manufacturers vs coronavirus 2020
On the surface, it looks like something from a movie set; a set of hand-sketched drawings that show off Ford’s plans to build a ventilator that could be used by health workers tending to sick patients afflicted by Covid-19.
A seat blower fan from the F-150 pick-up truck, a plastic backing plate and a brace of tubes all powered by a power drill battery combine neatly on paper in a noble effort to answer the call from an increasingly desperate nation, where if the coronavirus virus gets away from the medical fraternity it could reportedly claim more than two million lives.
The problem with Ford’s magnanimous gesture is that while the drawings came together in a couple of days, a viable ventilator product won’t likely surface until June at the earliest.
Why the delay? It’s not the fans, obviously – Ford can whistle up enough fans from a supply chain that provides enough trucks for Ford to sell more than 2400 every single day in the US.
And with every plant standing idle, there are plenty of bodies to apply to the task of building them, and a typical car factory has enough space that can be used as clean rooms for assembly. The capacity to print 3D parts at scale is also a big advantage.
The car industry and coronavirus: why the world’s car factories have fallen silent
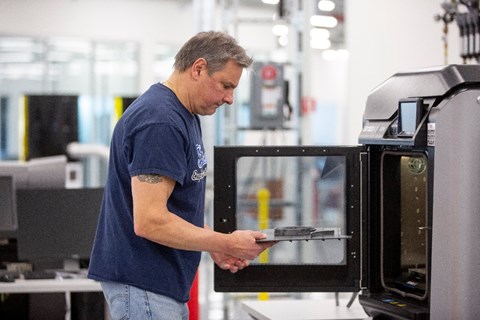
The other parts, like hoses and seals, are pretty straightforward – but the delay comes in the area of electronics. Outside suppliers will need to design and test the right parts, before manufacturing of the complete units can be facilitated.
Units will need to be prototyped and tested, too. Take into account the sheer numbers of people not actually at work at the moment, and it’s easy to see where delays and bottlenecks might occur before completion.
MoT tests suspended for six months owing to Covid-19
Tesla, GM join Ford and Dyson in bid to make ventilators for coronavirus pandemic
Others are doing their bit; General Motors, for example, is using its sheer size and muscle to help a company called Ventec build up to 200,000 of its ventilators, using GM’s purchasing power and factories.
It claims it has 95 percent of the parts needed to push the project forward, but others aren’t due to ship until April and beyond.
Even Tesla’s Elon Musk – who was just days ago scoffing at the idea of the danger – flew in 1000 ventilators from China, but it’s a literal drop in the bucket. New York governor Andrew Cuomo says the city needs 60,000… and that’s just one city in a country of 325 million people.
Building ventilators is not like slinging toasters together. US-based ventilator maker Medtronic, for example, has pushed its output from 100 to 225 units a week but needs to source 1500 parts from 14 different locations for each one, in a time when logistics management is a huge challenge.
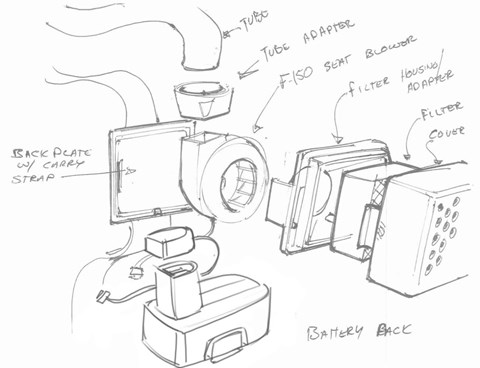
The ventilator issue is a critical one. The devices are used to pump oxygen in and remove carbon dioxide from sick patients’ lungs, but currently, there simply aren’t enough in circulation.
Even though ventilator makers have doubled their output, part shortages mean that the projected spike in Covid-19 cases will have torn through the country by the time enough is ready.
US stocks currently stand at 160,000 nationwide, standing in the way of a virus that could infect millions of Americans.
Coronavirus and the car calendar: all the events, motor shows and races cancelled and postponed
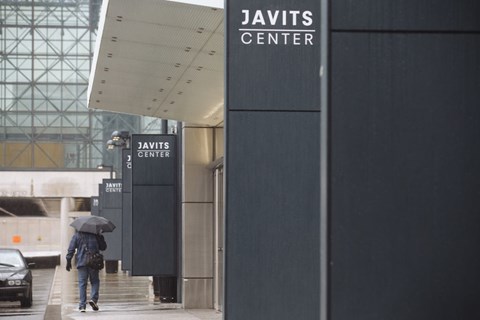
Underpinning the whole issue is the unwillingness of the Trump administration to invoke something called the Defense Product Act, which compels private companies to build products for the good of the country and provides investment to speed the process along.
Hopefully, Ford – in conjunction with its partner GE Healthcare – can make swift headway, but this fight against an invisible, microscopic enemy may be over before it’s even really begun.
What to do if you need a payment holiday owing to coronavirus: your rights as a PCP owner