► Exclusive access to Bentley’s factory
► See how the new Bentayga SUV is built
► Get the lowdown on the new luxury SUV
In the old brick buildings that assembled the Rolls-Royce Merlin engines which powered Spitfires to World War Two glory, they’re creating the biggest, fastest, most luxurious SUV yet: Bentayga. We have exclusive access to the car, and the craftsmen making it.
At one stage it seemed probable that the new Bentley Bentayga would be built far away in Bratislava. To many top managers in the Volkswagen Group’s Wolfsburg HQ, the Slovakian plant made good sense. Are not all the group’s other large SUVs – from Cayenne to Q7 to Touareg – all built in this state-of-the-art plant, where the buildings are new and the labour rate is less than half that of the UK’s? (Ironically, at the same time the Bentayga is launched, Jaguar Land Rover announces it will build cars in Slovakia, no doubt attracted by the combination of high tech and low cost.)
So the Bentayga very nearly became the first Bentley built outside the UK. In the end, common sense – and a dash of Bentley’s never-ending obsession with heritage – prevailed. The old Crewe factory was reconfigured (at a cost of £115 million) and Bentayga came to Britain. David Cameron even ventured up north to make the happy announcement, standing alongside all the smiling umlauts on Bentley’s German-dominated management board.
And it’s quite a car. The name is curious and strangely contrived, for a company that so clearly values authenticity; it’s also an odd departure from mellifluous and history-imbued badges such as Continental GT, Mulsanne and Arnage. You’ll recall the first prototype, shown at Geneva more than three years ago, was also not well received, a vast, vulgar, glitzy bling barge, clearly aimed at flaunting oligarchs and showy Sheiks.
Well, the production car is no beauty but it’s a whole lot easier on the eye than that unsightly EXP9F concept. We find a typically big and bluff Bentley nose – a chromed White Cliff of Dover and a clear warning to slower cars to vacate the fast lane, and pronto. We find appealing Bentley-style hips, chunky shoulders, vast bonnet (accommodating an equally vast 12-cylinder engine) and a long rear overhang, for a sportier and more streamlined stance. As an SUV, it is a two-box car, a Bentley first. It’s the first Bentley with a tailgate.
As a Bentley, it also subscribes to Oscar Wilde’s philosophy that nothing succeeds like excess. It’s the fastest, most luxurious, most expensive, most powerful and most exclusive production SUV in the world. Project director Peter Guest says it’s the first of a new breed of car, the ultra-luxury SUV, as Bentley tries to position the Bentayga north of the poshest Range Rover and Cayenne. Lamborghini and Rolls-Royce, we now know, will follow into this rarefied market, diamonds in the rough.
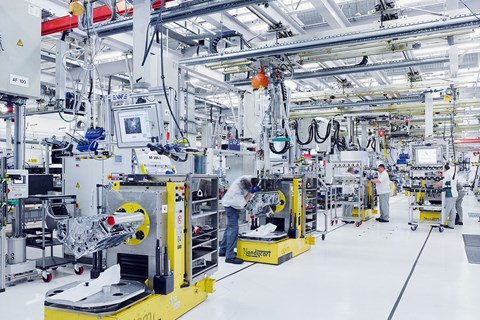
Bentayga pricing and engine specification
The Bentayga will be priced at £160,200, or at $185,000 in its biggest market, the USA. It’s the world’s only 12-cylinder SUV, good for 600bhp, and a massive 664lb ft of torque. The W12 engine is, surprisingly, all new – lighter and more efficient than the current W12 which, for the time being, continues to provide service in Continentals and the priciest Audis.
That new W12 is hand-assembled in Crewe (like the old W12), and is clearly the prime source of the Bentayga’s domineering performance. Its other clear area of leadership – not surprising when you consider the price – is its craftsmanship, long a Bentley speciality. Only Rolls-Royce can match Bentley’s standards here. To appreciate this fully, you need to venture inside those old brick buildings in Crewe, far removed from the clinical excellence of a ‘normal’ mass-production car factory.
Here, where those 12-cylinder Merlin WW2 engines were made, and many generations of finely crafted Rolls-Royces and Bentleys were produced, the Bentaygas are assembled, including the hand-crafted leather and wood, the largely hand-made W12s, and final assembly of the car, including painting.
Crewe, home of Bentayga production
Crewe has had its ups and downs over the years but it’s fair to say that the mood now at Volkswagen’s north-west European outpost – VW’s Winterfell – has never been more upbeat. (Ironically, Crewe was originally chosen as a factory location partly because it was a long way from Germany – so further for the Luftwaffe to fly to bomb it.)
The Bentayga alone creates 400 new jobs at Crewe, and almost single-handedly doubles production. A factory built for war is now enjoying the fruits of a prosperous peace, ironically thanks to German investment. Much of its structure is still original, including the stained brick walls and much of the roof frames – pitched like a row of terrace houses to try to confuse the Germans (the Luftwaffe, not Volkswagen). There is even a vaguely old-fashioned smell of oil and grease and dust and glue and paint, with a slight whiff of leather and dried wood.
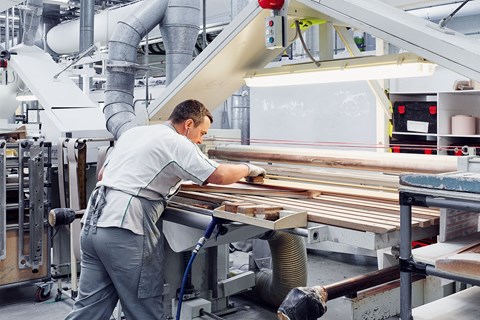
The old brick buildings give no indication of the magic wrought behind the walls. Only the occasional new Bentley parked, or driven slowly, around the warren of lanes suggests something special. Step inside these old halls and you enter a different world of car manufacturing. You see craftsmen stitching and cutting, not robots welding; you see rows of ladies (no men!) sitting at quietly thrumming sewing machines; giant fragrant hides being inspected by expert eyes and hands; stacks of delicate thin wood veneers – exquisitely patterned – that come from California, Canada, China and Spain, laser cut but hand polished, tech meets trad. It’s more like an upmarket furniture factory than a car plant.
In another building, giant Bentayga frames slowly morph from Slovakian skeletons – the body’s core aluminium structure comes from Bratislava, so those opportunistic Slovaks didn’t totally miss out – into beautifully finished Bentleys. There are some lovely exterior design details, proof of the fanatical attention that goes into a Bentayga. My favourite are the dainty headlamp washer caps in the middle of the smaller front lights, reducing design clutter. They jump to attention when there’s water to be sprayed. I also love the Winged Bs on the flanks, the ‘B’ graphics in the taillights and the vast sculptural (aluminium) front wings, unencumbered by shutlines around the headlamps (much harder to manufacture this way).
Inside the Bentley Bentayga
Though there are attractive flourishes on the exterior, the car’s highlight is its cabin. Step inside a Bentayga after a Q7 or a Cayenne, and it’s like stepping into a palace from a penthouse: polished, hand-crafted tradition versus precise, mass-produced technology.
There are so many delicious features, from the diamond quilted leather seats (made in-house by Bentley), the bulls-eye vents manufactured from solid aluminium, plus the three delicate rows of beautifully tactile knurling on the vent controls, gearlever and clock bezel (all real alloy, not plastic). The vent controls are organ-stop, and glide as if lubricated by oil. They slide without notch, beautifully damped. The speakers are covered in real metal fabric. There is little sign of plastic: Bentley starts with leather. A vast panoramic sunroof allows light naturally to illuminate this most splendid of SUV cockpits.
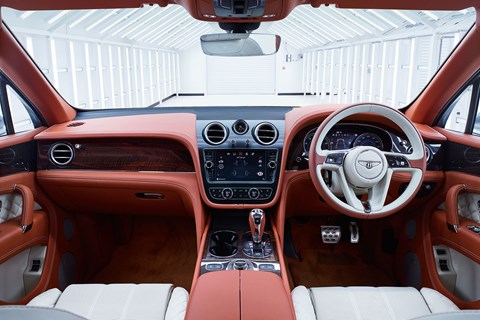
Dave Hudson, manufacturing project leader, guides us around the old Crewe buildings where the magic happens. The woodshop uses walnut from Californian orchards, chestnut from Europe, olive ash from Europe, tamo ash from China, fiddleback eucalyptus from Spain and birds-eye maple from Canada: seven different veneers are offered on the Bentayga. There is more wood in a Bentayga than any other Bentley, for the simple reason it has the biggest cabin. Walnut – sliced from the root balls of old fruit trees – will likely constitute 60% of sales. The wood is all hand-polished and sanded; they are never bleached or stained on a Bentley. One tree will trim 50 cars, and each car always uses wood from the same tree, for consistency.
In the adjacent leather shop Richard Priest, operations manager, tells us each Bentayga uses 14 hides (a Continental GT uses nine). They are all from large southern German bulls: about 5000 hides a week will be used by Bentley in total, after the Bentayga is launched. Craftsmen carefully examine each hide, cutting out the warts, boils and growth lines.
Assembling the Bentayga’s interior
It takes five hours to hand-stitch the leather for each steering wheel, and 37 hours to cross-stitch the seats. The diamond quilt 4 pattern is machine stitched. So is the Bentley wings motif in the seatback (it has 5498 individual stitches). The cross- and contrast-stitching are always hand-sewn; apparently the craftsmen can recognise their own work.
Bentley makes its own seats – very unusual in the car industry – and we see throne-size chairs taking shape, skinned in either diamond-quilted or straight flute upholstery, always in lustrous leather, of course. In the four-seat versions, the front and rear seats are identical.
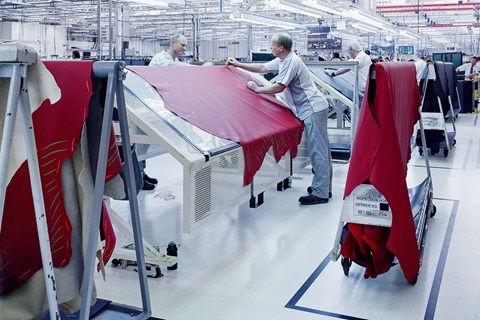
Separately, we see a glueing machine affixing carpet to the back of the rear seats of the five-seat versions. These chairs fold forward 60:40. In effect, the Bentayga is Bentley’s first hatchback, so folding rear-hatch-style seats are a novelty. This carpet-glueing technique – disappointingly automated – comes from those masters of mass manufacture at Audi. The Bentley craftsmen seem surprisingly pleased with it, a new 21st century toy in a manufacturing environment that is otherwise unremittingly last century.
In a separate old brick structure, the W12 engines are assembled, turbochargers, camshafts, pistons, valves, fuel rails and timing covers (and many other components) all fitted by hand. Shaun McNeil, head of engines, tells us that it’s 26kg lighter than the old W12: block, head, pistons and bearings are all new, so this is far more than an extensive revamp. Fuel economy and CO2 emissions, says McNeil, have improved by 10%. CO2 emissions will be 292g/km, not that too many Bentayga owners will care.
If the production process is Bentley-familiar, the segment in which it competes clearly is not. Yet, says project director Guest, Bentley expanding into SUVs was an obvious step. ‘It’s a fast-growing segment, most of our customers already own one [typically a Range Rover in the UK, often a Cadillac Escalade in America], and it’s a strong brand fit. Put it this way: if WO could do a car today, he’d do an SUV.’
More surprising is the effort they’ve put into its off-road credentials. While Guest admits that ‘rock crawling isn’t likely’, the Bentayga is designed to cope with Dubai dunes, Saharan sand, Siberian snow, Midlands mud plus rutted gravel drives on that bumpy journey to the front door of your New England log cabin or your out-of-Moscow dacha.
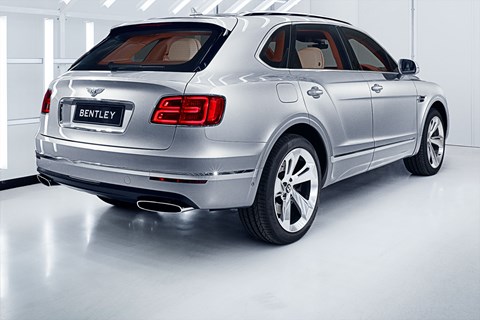
New Bentley features
Bentley’s new Drive Dynamics control – like Land Rover’s Terrain Response but with added programmes – gives eight choices, to provide ideal performance either on- or off-road. In the rough, we find programmes for sand, mud and ruts, gravel, plus snow and grass. A top-view camera helps the driver become his own off-road spotter. On the tarmac – where the Bentayga will clearly spend most of its life – we find settings to optimise performance or comfort, plus an all-encompassing ‘Bentley’ mode (which Guest recommends for day-to-day use) and a customised setting, to enable you to mix and match (sharper throttle, softer damping, for example).
Air springs are standard and there are four ride heights, including a ‘kneel’ setting to make getting in and out easier. You can also dip the rear while maintaining front ride height, all the better for hitching that horsebox. It’s a practical car as well as a posh one: towing capacity is 3.5 tonnes.
The four-wheel-drive system is fully mechanical, runs full-time, and is similar to that in the latest Audi Q7. It’s mated to an eight-speed ZF gearbox, with central Torsen diff. A low-range system, as on a Range Rover, was considered but rejected, partly because of the weight (and, I suspect, the unlikelihood that a customer would ever use it). ‘To be honest, the car doesn’t need it,’ Guest tells me. ‘The W12 has so much torque, it’s simply unnecessary.’ Diff locks, equally, were considered and rejected. ‘With modern electronics, they’re not needed.’
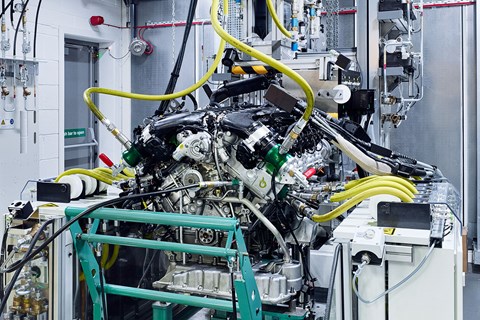
As proof of its substantial off-roading credentials, the Bentayga can wade to a depth of 500mm. Guest admits it can’t compete with a Range Rover off-road. ‘That wasn’t our goal: substantial all-terrain capability was.’ A Rangie can wade to a boat-like 900mm, and also has superior approach and departure angles, due to shorter overhangs, especially at the rear.
Rather, it’s in on-road performance that the Bentayga can trump all. With a 600bhp engine, a chassis tagged ‘Bentley Dynamic Ride’ (powered by a mighty 48-volt system complete with electrically adjustable anti-roll control to combine vertical suppleness and lateral stiffness) plus a Range Rover-like all-aluminium body and chassis to cut weight (the target is a Range Rover-like 2400kg), the Bentayga should perform like no SUV before or since: Lambo meets Landie. Maximum speed is an astonishing 187mph and the 0-62 dash is covered in 4.1 fast-moving seconds.
Finally, let us return to those hallowed halls, built on a former potato field, to make aero engines to defend the realm. Though ‘made in Crewe’, most of the major mechanical components that constitute a Bentayga actually come from Germany. This includes block, heads and crankshaft. Britain, it seems, does not have the manufacturing capability to make big castings in big volumes. Crewe may be the kings of hand craftsmanship. But when it comes to machine mass production, Germany still reigns supreme.
Bentley Bentayga: highlights of the build process
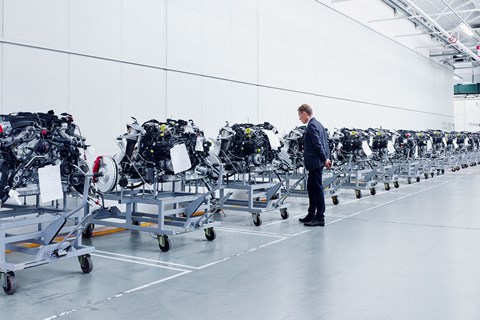
The engine: Built in 264mins
The W12 engine has been totally redesigned for the Bentayga and all major components – including block and heads – are new. It’s 26kg lighter, and has 10% lower CO2 emissions. Unusually, it has both direct and indirect port fuel-injection to improve efficiency, throttle response and emissions. Fuel-injection pressure is much higher, further improving efficiency.
Eleven people work on the engine assembly line, one per station – and the engine goes through 11 stations, spending 24 minutes at each assembly point. Most components are fitted by hand, including pistons, valves and camshafts. The W12’s big advantage over a V12 is that it’s 25% shorter. It is largely designed and engineered in Crewe, by Bentley’s burgeoning engineering team, although nearly all big components – including aluminium castings for block and heads, and the turbos – come from Germany. The V8s used in some Continentals – due to appear in future Bentaygas – are Audi designed, and come from Hungary.

The veneer: 50 cars per tree
The wood veneers come from around the world: walnut from Californian orchards, fiddleback eucalyptus from Spain, tamo ash from China, and more. Seven different types of veneer are offered on the Bentayga at launch, and more are likely to follow. Walnut is likely to constitute 60% of demand; it’s also the most popular wood in other Bentley models. The burr walnut comes from the root balls of old trees, cut into thin veneers: 24 sheaths are used per car, always in a ‘mirror image’ (to give a completely symmetrical look to the cabin), and always from the same tree. One tree will trim about 50 cars.
Bentley specialists visit wood suppliers from around the world – typically in Valencia, Milan and London – selecting the very best veneers, and every 18 months or so they’ll introduce a new one. The veneers are cut by laser and – unlike the wood used by many rivals – are never bleached or stained. One change for the Bentayga is the use of ovens to cure the lacquer in two hours: hitherto it took three days for natural curing. Quality of finish is unaffected, they insist.
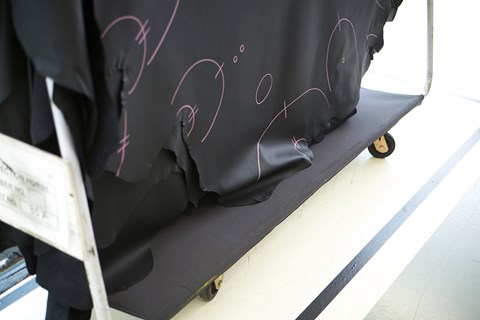
The leather: 100% German bull
Bentley has the best leather in the car industry, and is renowned for the quality of its craftsmanship. All hides come from southern German bulls, which are especially beefy. The hides come treated and prepared from Germany, to Crewe, where the craftsmen cut, fit and stitch them. On a Bentayga 14 hides are used, compared with nine for a Continental GT and 12 for a Flying Spur. The craftsmen closely inspect the hides by hand and eye, marking imperfections before they’re machine-cut to a range of patterns. Only about 60% of the hide is deemed good enough for use in a car.
There are 18 different hues of leather – more if you want to go down the Mulliner bespoke route. After the Bentayga goes into full production, Bentley will use about 5000 hides a week – almost double current demand. The stitching of the leather is done partly by machine, and sometimes by hand. Bentley designs and makes its own seats – unusual in the car industry.
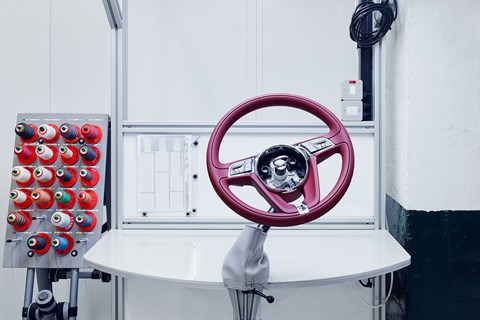
The cabin: Posher than posh
The Bentayga’s cabin is the most luxurious ever found on an SUV, perhaps not surprising at £160,200. Leather and wood is used throughout for the trim, and when you see silver it’s nearly always real alloy, not plastic. The vents, for instance, are milled from solid aluminium. Specially delightful touches include the precise triple-row knurling around the bullseye vents, clock bezel and gearlever. The air vents, in time-honoured Bentley practice, are organ-stop controlled, and slide as though in oil. The steering wheels are all hand-stitched, in one of the most time-consuming parts of the assembly: each wheel takes five hours to swathe with leather. Elsewhere, stitching is sometimes done by machine, sometimes by hand. The cross- and contrast-stitching is always hand done, and apparently individual craftsmen can recognise their own work. Diamond quilt upholstery – machine stitched – is standard on the Bentayga, though straight fluting is also available. ‘Comfort’ and ‘Sports’ seats are offered. Eighteen people hand-build the Bentayga’s seats.
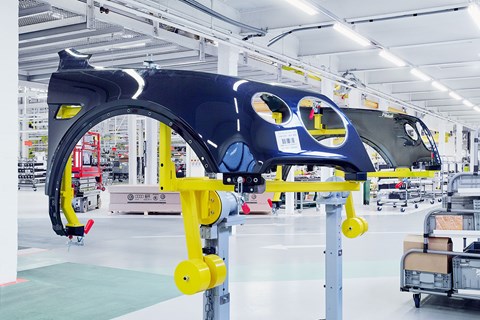
The Bentayga: It’s a plastic grille?
After painting, the Bentayga is inspected for any flaws. The exterior design DNA is very Bentley, from upright ‘chrome’ grille (made from plastic, slightly disappointingly – it’s better for pedestrian protection) to chunky shoulders to the big squared haunches. Note central ‘caps’ in smaller headlamps – these are the integrated washers, a really nice design detail. The headlamps are LED matrix beam, a technology first shown in latest Audi A8. Note also bumperless nose, for a cleaner style.
The body is all aluminium, as is nearly all the chassis (like a Range Rover), bonded, riveted and with some welding. This gave a 250kg weight saving over an equivalent size steel body. There are some borrowings from the Audi Q7/VW Group SUV platform, but mostly Bentayga is bespoke. Bodies come from same Slovakian factory as Q7 and Cayenne to Crewe for final assembly. Three wheel sizes are offered, the biggest 22in for road use. Surprisingly, Bentayga has been engineered for real off-roading, when fitted with smaller wheels. Bentley’s version of Land Rover’s Terrain Response – Drive Dynamics – has four off-road settings.
Read our full Bentley Bentayga review